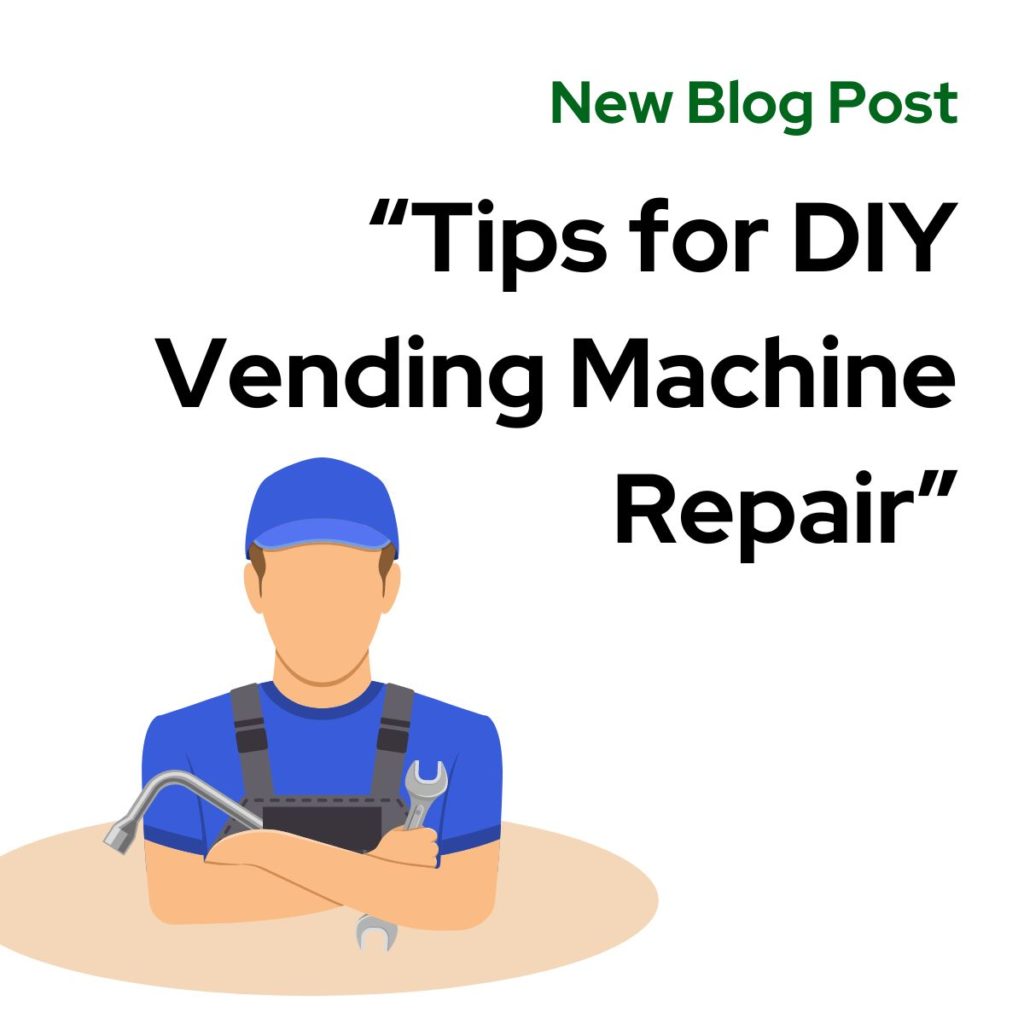
Vending machines are a staple in many workplaces, schools, and public spaces, providing convenient access to snacks, drinks, and other items. However, like any piece of machinery, vending machines can experience issues that require maintenance or repair. While some problems may necessitate professional assistance, there are many common issues that can be resolved with a bit of DIY knowledge. In this blog post, we’ll explore some practical tips for DIY vending machine repair, helping you save time and money by addressing issues yourself.
1. Understanding the Basics of Vending Machine Operation
Before diving into repair tips, it’s important to have a basic understanding of how vending machines operate. Most vending machines consist of several key components, including:
- Control Board: The control board is the brain of the vending machine, managing all of its functions, from accepting payments to dispensing products. If the control board malfunctions, it can cause a variety of issues.
- Coin and Bill Mechanisms: These mechanisms are responsible for accepting and processing payments. They can become jammed or malfunction, preventing customers from making purchases.
- Dispensing Mechanism: This is the part of the machine that physically delivers the product to the customer. Issues with the dispensing mechanism can result in products getting stuck or not being dispensed at all.
- Refrigeration System: In machines that offer chilled products, the refrigeration system keeps items cool. Problems with the refrigeration system can lead to items not being kept at the correct temperature.
- Display Panel: The display panel provides information to customers, such as product prices and error messages. If the display is not functioning properly, it can cause confusion and frustration for users.
2. Common Vending Machine Issues and How to Fix Them
Now that you have a basic understanding of vending machine components, let’s look at some common issues and how to address them.
- Problem: Machine Not Accepting Payments
If your vending machine is not accepting coins or bills, there are a few potential causes to investigate:
- Check for Jams: Coins or bills can sometimes become jammed in the payment mechanisms, preventing the machine from accepting further payments. Open the machine and inspect the coin and bill mechanisms for any obstructions. Remove any jammed items carefully.
- Clean the Mechanisms: Dirt and debris can accumulate in the coin and bill mechanisms, causing them to malfunction. Use a soft cloth or compressed air to clean the mechanisms and remove any buildup.
- Test the Sensors: Many vending machines use sensors to detect coins and bills. If these sensors are dirty or misaligned, they may not function properly. Clean the sensors and check that they are properly aligned.
- Problem: Products Not Dispensing
If products are not being dispensed when selected, there are several potential issues to consider:
- Check for Jams: Products can sometimes become stuck in the dispensing mechanism, particularly if they are not properly loaded. Open the machine and inspect the dispensing mechanism for any obstructions. Clear any jams and ensure that products are loaded correctly.
- Inspect the Motor: The dispensing mechanism is typically powered by a motor. If the motor is not functioning, the machine will not dispense products. Test the motor by running a manual cycle to see if it operates correctly. If the motor is not working, it may need to be replaced.
- Examine the Control Board: If the control board is malfunctioning, it may not be sending the correct signals to the dispensing mechanism. Inspect the control board for any visible signs of damage, such as burnt components or loose connections. If necessary, replace the control board.
- Problem: Machine Not Cooling
If your vending machine is not keeping products cool, the refrigeration system may be at fault:
- Check the Power Supply: Ensure that the machine is properly plugged in and receiving power. If the machine is not receiving power, check the circuit breaker or fuse box to ensure that there are no issues.
- Clean the Condenser Coils: The condenser coils are responsible for dissipating heat from the refrigeration system. If the coils are dirty or blocked, the system may not cool effectively. Clean the coils with a brush or vacuum to remove any dirt or debris.
- Inspect the Refrigerant Levels: If the refrigerant levels are low, the machine may not cool properly. While checking and refilling refrigerant typically requires a professional, you can inspect the system for any obvious signs of leaks or damage.
- Problem: Display Panel Not Working
If the display panel is not functioning or showing error messages, you may need to troubleshoot the following:
- Check the Connections: Loose or damaged connections can cause the display panel to malfunction. Open the machine and inspect the wiring to ensure that all connections are secure and intact.
- Reset the Machine: Sometimes, a simple reset can resolve issues with the display panel. Turn off the machine, wait a few minutes, and then turn it back on to see if the problem is resolved.
- Replace the Display Module: If the display panel is damaged or not functioning, it may need to be replaced. Consult the machine’s manual for instructions on how to replace the display module.
3. Maintenance Tips to Prevent Common Issues
Regular maintenance is key to keeping your vending machine in good working order and preventing common issues. Here are some maintenance tips to help you avoid costly repairs:
- Keep the Machine Clean: Regularly clean the exterior and interior of the machine to prevent dirt and debris from accumulating. Pay special attention to the coin and bill mechanisms, sensors, and condenser coils.
- Check the Stock Levels: Ensure that products are properly loaded and not overcrowded, which can cause jams in the dispensing mechanism. Rotate stock regularly to prevent items from expiring.
- Test the Machine Regularly: Periodically test the machine by making a purchase to ensure that all components are functioning correctly. This will help you identify any potential issues before they become major problems.
- Monitor Temperature Settings: If your machine has a refrigeration system, monitor the temperature settings regularly to ensure that products are being kept at the correct temperature. Adjust the settings as needed based on the ambient temperature and product requirements.
- Replace Worn Parts: Over time, components such as belts, motors, and sensors can wear out and may need to be replaced. Keep an eye on these parts and replace them as needed to prevent breakdowns.
4. When to Call a Professional
While many vending machine issues can be resolved with DIY repairs, there are times when it’s best to call a professional. Here are some situations where professional assistance may be necessary:
- Electrical Issues: If you suspect that the machine has electrical problems, such as faulty wiring or a short circuit, it’s best to call a professional electrician to avoid the risk of injury.
- Refrigeration Problems: If your machine’s refrigeration system is not working and basic troubleshooting hasn’t resolved the issue, you may need to call a professional technician who is qualified to handle refrigerants and complex cooling systems.
- Complex Repairs: Some repairs, such as replacing the control board or major components, may require specialised knowledge and tools. If you’re not comfortable performing these repairs yourself, it’s best to seek professional help.
5. The Importance of Having the Right Tools
Having the right tools on hand can make DIY vending machine repair much easier. Some essential tools to consider include:
- Screwdrivers: A set of screwdrivers, including both flathead and Phillips head, is essential for opening the machine and accessing its components.
- Multimeter: A multimeter is a handy tool for testing electrical components, such as the control board, sensors, and wiring.
- Compressed Air: Compressed air is useful for cleaning out dirt and debris from hard-to-reach areas, such as the coin and bill mechanisms.
- Pliers: Pliers are useful for gripping and manipulating small components, such as wires and connectors.
- Manuals and Documentation: Always keep the machine’s manual and any relevant documentation on hand. These resources provide valuable information on troubleshooting and repair procedures.
6. Safety Considerations
When performing DIY vending machine repairs, safety should always be a top priority. Here are some safety tips to keep in mind:
- Turn Off the Power: Always turn off the power to the machine before performing any repairs or maintenance. This will help prevent electrical shocks and other injuries.
- Use Proper Tools: Use the correct tools for the job and ensure they are in good condition. Using the wrong tools or damaged tools can lead to accidents.
- Work in a Well-Lit Area: Ensure that you have adequate lighting when working on the machine. Poor lighting can increase the risk of mistakes and injuries.
- Follow Manufacturer Instructions: Always follow the manufacturer’s instructions and guidelines when performing repairs. This will help ensure that the repair is done correctly and safely.
DIY vending machine repair can be a cost-effective way to keep your machines running smoothly and minimise downtime. By understanding the basics of vending machine operation, troubleshooting common issues, and performing regular maintenance, you can address many problems on your own. However, it’s important to recognise when a repair is beyond your skill level and when it’s time to call in a professional. With the right tools, knowledge, and safety precautions, you can successfully tackle many vending machine repairs and keep your machines in top condition.